2024.04.08
工場の大規模修繕工事の内容は?流れや修繕内容は?
大規模修繕や防水工事のご相談は実績豊富な新東亜工業へ

工場の大規模修繕工事は、老朽化対策や生産効率向上を目的に実施されます。計画立案から工事完了までには、現地調査、設計、資材調達、施工、検査といった各工程が含まれます。
今回は工場における大規模修繕について解説したいと思います。
工場の大規模修繕が必要な理由
工場は生産設備や建屋を長期間使用するため、経年劣化による老朽化が進行します。
工場の安全運転や製品の品質を維持するためには、定期的な大規模修繕工事が不可欠です。
主な理由は以下の通りです。
- 生産設備の故障リスク低減
設備の老朽化が進めば、故障の発生リスクが高まります。東京商工リサーチによると、2019年の国内製造業の設備故障による損失額は約4,000億円と試算されています。定期的な修繕により、故障リスクを最小限に抑えることができます。 - 製品の品質維持
老朽化した設備では、製品の品質や生産性が低下します。グローバル化が進む中で、高品質な製品を効率的に生産する必要があります。 - 法令遵守
労働安全衛生法や消防法などの法令で、設備の定期点検・修繕が義務付けられています。法令違反には、営業停止処分といった厳しいペナルティが課されます。
以上のように、工場の大規模修繕は安全性と生産性を維持するために欠かせません。
時宜を逸することなく、計画的に実施する必要があります。
工場の大規模修繕の周期やタイミングは?
工場の大規模修繕の周期は、業種や設備の種類によって異なります。一般的には、以下のような周期で大規模修繕が行われています。
- プラント設備 : 4~5年周期
- 生産設備(工作機械など) : 5~7年周期
- 建屋 : 10~15年周期
これは、設備メーカーの推奨値や、過去の修繕実績から定められた目安です。
具体的な周期は、設備の使用頻度や環境条件によっても変わってきます。
周期が短すぎると修繕コストがかさみ、長すぎると故障リスクが高くなるため、適切な時期に修繕を行うことが重要です。
設備の保全担当者は、日頃からメンテナンスデータを収集・分析し、最適な修繕時期を判断する必要があります。
工場や倉庫は、長年使用することでさまざまな経年劣化が発生します。そのため、適切なタイミングで修繕・改修工事を行うことが重要です。
雨漏りが発生したり、外壁がひび割れたり、屋根材が剥がれてきた場合は、早急な修繕が必要です。また、外壁材や屋根材の寿命が過ぎている場合や、塗装が色褪せてきた場合なども、修繕・改修工事を行うべきタイミングです。
大規模な修繕・改修工事には多額の費用がかかりますが、将来的に大きなトラブルや損失を防ぐことができます。また、設備の更新や省エネ対策などの改修工事を行うことで、生産性や効率を向上させることも可能です。
工場の大規模修繕の修繕箇所と内容
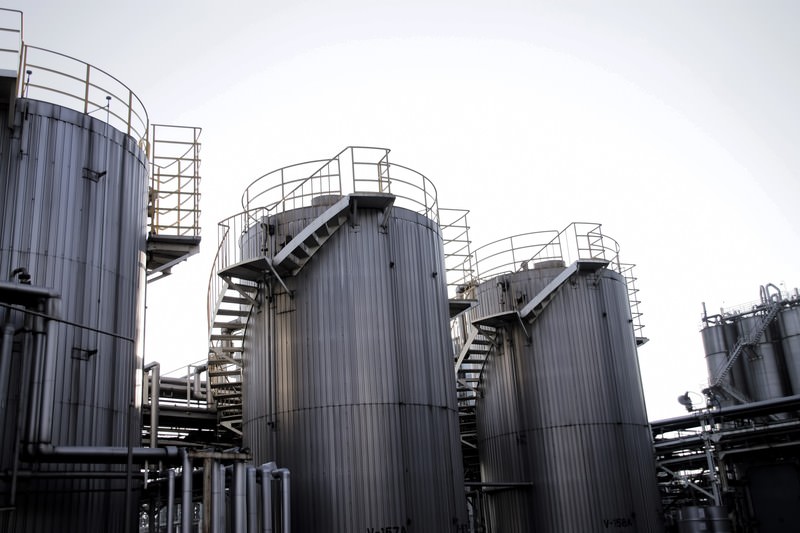
大規模修繕では、プラント全体や生産設備、建屋など、様々な箇所が対象となります。
主な修繕箇所と内容は以下の通りです。
【生産設備】
- 動力伝導部(ベアリング、歯車、チェーン等)の分解清掃・交換
- 制御・電気系統(モーター、インバーター、配線等)の点検・交換
- 本体フレームの劣化部位の補修
【プラント設備】
- 反応塔、熱交換器等の内部水洗と点検
- ポンプ、圧縮機等の分解点検とオーバーホール
- 配管系統の肉厚検査と補修
【建屋】
- 外壁、屋根、床の劣化部分の補修や防水工事
- サッシ、シャッターの交換
- 電気設備、空調設備の更新
このように、消耗・劣化の著しい部品や部位を中心に、分解点検や部品交換が行われます。
必要に応じて、機能の向上や更新も並行して実施されます。
工場の大規模修繕の費用
大規模修繕工事には多額の費用が掛かるため、修繕費用の見積りと費用対効果の検証が重要です。
修繕費用は工場の規模や設備の種類によって大きくばらつきますが、一例として以下の様な金額になります。(※設備更新費用は除く)
- 中小プラント : 数千万円~2億円程度
- 大規模プラント : 10億円~30億円程度
- 生産設備(工場全体) : 数億円~10億円程度
また、修繕に伴う機会損失(操業停止による売上損失)も大きな費用負担となります。
よって、修繕期間の短縮が課題となっています。
費用対効果の検証では、修繕後の設備の延命年数や生産性向上効果を金額換算し、費用に見合うかを判断します。
長期修繕計画を立て、優先順位をつけながらコストを最適化していく必要があります。
修繕には多額の予算を要しますが、安全運転と製品の品質確保のため、欠かせない投資だと認識すべきです。
工場の大規模修繕の流れや進め方
工場の大規模修繕工事は、計画的な進め方が重要です。
期間や費用、品質などを最適化するには、体系的な工程管理が不可欠となります。
一般的な大規模修繕の進め方は、以下の流れとなります。
工場の大規模修繕の流れや進め方1【事前調査・計画段階】
- 修繕対象設備の点検・診断
- 修繕工事の要否、範囲、時期の検討
- 工期・工程の策定
- 修繕内容・費用の見積り
- 修繕計画の承認・予算化
事前に十分な調査と計画を立てることが肝心です。
修繕の要否判断は、法令や設備メーカーの推奨基準、設備診断結果に基づいて行います。
工期は生産計画との調整が必要不可欠です。
工場の大規模修繕の流れや進め方2【発注・準備段階】
- 修繕業者の選定・発注
- 修繕部品・資材の手配
- 作業員の確保・安全教育
- 仮設備の設置
適切な修繕業者の選定と、部品の確実な調達が重要です。
また、修繕作業に伴う安全リスクへの対策も欠かせません。
仮設備も必要に応じて十分に準備する必要があります。
工場の大規模修繕の流れや進め方3【実施段階】
- 設備の分解・点検
- 部品の交換・補修
- 組立て・試運転
- 品質・性能の確認
作業の標準化と安全対策を徹底した上で、確実な品質で修繕を実施します。
分解・組立て作業は、マニュアルと熟練作業員の指導の下で行います。
最終的には設備の性能試験を行い、所定の仕様を満たしていることを確認します。
工場の大規模修繕の流れや進め方4【事後対応】
- 修繕実績の記録と保存
- 次回修繕計画の見直し
修繕工事の経験を次回に生かすため、作業実績を記録・保存することが重要です。
今回の反省点を踏まえ、より良い次回の修繕計画を立案する必要があります。
このように、修繕工事は綿密な事前調査と計画から始まり、安全で着実な作業工程を経て、最後は実績のフィードバックへとつながる、一連の流れがあります。
各ステップを確実に進めることで、無事故・高品質の修繕を実現することができます。
工場の大規模修繕の注意点
工場の大規模修繕には、さまざまな注意点があります。
間違えれば、重大な事故や多額のロスを招く可能性があるため、以下の点に十分留意する必要があります。
【安全対策】
修繕作業では、転倒・落下・切傷・感電・火災などの人身事故や設備損傷の危険性が高まります。適切な安全対策を講じることが何より重要です。
- 安全教育の実施
- 保護具の着用徹底
- 作業手順の標準化と遵守
- 火気・電気の安全管理
- 救急体制の確保
【品質管理】
修繕品質が不十分な場合、生産トラブルや製品の不具合を招きます。
修繕業者の選定と作業管理、実績の評価を徹底する必要があります。
- 修繕業者の技術力と実績の確認
- 作業手順・品質基準の遵守
- 管理者による徹底した監視・検査
- 記録の保存と次回への活用
【工程管理】
修繕工期の延長は、多額の機会損失を生みます。
適切な準備と余裕を持った工程設定が求められます。
- 設備停止時期の最適化
- 部品調達期間の確保
- 作業手順の標準化・マニュアル化
- 定期的な工程進捗の確認
【費用管理】
予算の準備不足や過剰投資は、経営に重大な影響を与えます。
適正な見積と費用対効果の検証が必要です。
- 修繕費用と延命年数の試算
- 優先順位付けと費用の最適化
- 予備費の確保
- 業者見積りの複数比較
このように、大規模修繕では様々な側面から、リスク管理と最適化が求められます。
それらを怠れば、工期の大幅な遅延、設備故障、人身事故、経営への打撃が生じる可能性があります。
計画的な注意深い対応が、何よりも肝心です。
まとめ
工場の大規模修繕工事は、老朽化した設備や建物を修復・更新することで、操業の継続や効率化、安全性の向上などを目的として行われます。 工事の内容は、建物の構造補強や外壁の修繕、屋根の葺き替え、設備の更新など、多岐にわたります。
修繕工事の流れは、まず現状調査を行い、必要な修繕箇所や内容を決定します。 次に、設計図面を作成し、必要な資材や人員を準備します。 そして、実際に工事を開始し、完了後に検査を行い、問題なければ完了となります。 工場の大規模修繕工事は、適切な時期に実施することで、操業の安定化やコスト削減、安全性の向上など、多くのメリットをもたらします。